Quality Welding Supplies to Equip Every Project with Precision and Safety
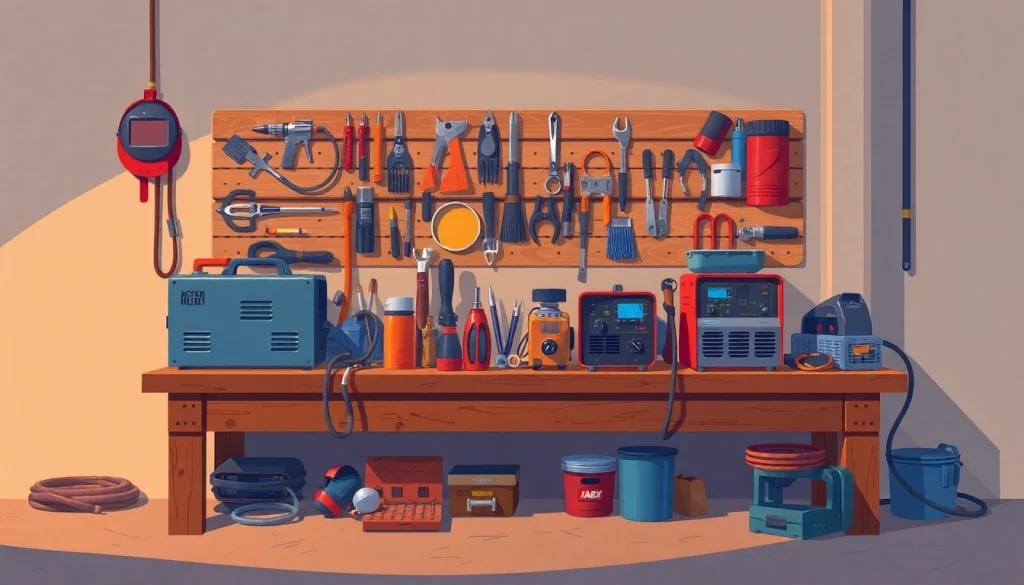
Understanding Welding Supplies
Welding is a critical process in various industries, encompassing metal fabrication, construction, automotive, and more. To execute quality welding, one must be equipped with the proper welding supplies, ensuring that both safety and execution meet industry standards. Understanding the essential components and types of welding supplies can significantly impact the effectiveness of your projects.
What are Welding Supplies?
Welding supplies include all materials and equipment necessary for conducting welding processes effectively and safely. This encompasses a range of items, from protective gear to welding machines, fillers, and more. The correct welding supplies directly influence the quality of the welds produced, affecting not only structural integrity but also the welder’s safety throughout the process.
Types of Welding Supplies Available
There is a plethora of welding supplies available on the market, differing by type, purpose, and welding processes utilized:
- Welding Machines: Such as MIG, TIG, Stick, and multiprocess welders.
- Protective Gear: Includes helmets, gloves, jackets, and respiratory protection.
- Consumables: Filler metals, welding wires, electrodes, and tips.
- Equipment and Accessories: Includes clamps, magnetic holders, and surface cleaning tools.
- Gas and Fuel: Depending on the process, acetylene, argon, and oxygen supplies may be necessary.
The Importance of Choosing Quality Supplies
Quality welding supplies are non-negotiable for achieving optimal results. Investing in high-quality materials and equipment not only enhances the welding output but also minimizes risks associated with faulty equipment or poor safety standards. Utilization of dependable supplies can result in:
- Increased Efficiency: Reliable equipment leads to fewer breakdowns and higher productivity.
- Improved Safety: Quality protective equipment safeguards operators against hazards.
- Better Weld Quality: Premium materials contribute to a stronger final product, reducing the likelihood of costly repairs.
Essential Welding Tools and Equipment
Protective Gear Every Welder Needs
Safety cannot be overstated in the welding environment. The right protective gear is critical to minimizing hazards:
- Welding Helmet: Essential for protecting the eyes from bright flashes and UVA/UVB radiation.
- Welding Gloves: Should be heat-resistant and flexible to ensure dexterity while protecting hands from burns.
- Welding Jacket: Fire-resistant jackets or coveralls protect the body from molten metal splatter and heat.
- Respiratory Protection: Depending on the materials being welded, respirators may be necessary to avoid inhaling harmful fumes.
Varieties of Welding Machines
Welding machines vary in functionality and application. Understanding these differences can help in selecting the right tool for your needs:
- MIG (Metal Inert Gas): Ideal for beginners, MIG welding is versatile and efficient for a variety of metals.
- TIG (Tungsten Inert Gas): Known for producing high-quality welds, TIG welding is preferred for thin materials and delicate work.
- Stick Welding: A traditional method suitable for outdoor use and heavy materials, often used in construction and repair work.
- Multiprocess Welders: These hybrid machines allow for different welding processes, providing versatility on jobsites.
Compliance and Safety Standards for Equipment
Adhering to industry standards and regulations is crucial in maintaining a safe working environment. Equipment and employees should comply with OSHA and ANSI guidelines, which encompass:
- Proper use and maintenance of protective gear.
- Regular inspections of welding equipment for safety.
- Training programs for personnel on safe welding practices.
Being aware of compliance not only protects workers but also ensures long-term success and sustainability of welding operations.
How to Purchase Welding Supplies Effectively
Selecting a Reliable Supplier
Choosing the right supplier is essential for accessing quality welding supplies. Here are some tips for selecting a reliable provider:
- Check Reputation: Look for suppliers with strong reviews and a history of reliability.
- Product Variety: A reputable supplier should carry a wide range of welding supplies to meet diverse needs.
- Customer Support: Good suppliers offer customer service that assists in product selection and post-purchase support.
Evaluating Prices and Product Quality
While it may be tempting to opt for the cheapest option, it is vital to balance cost with quality. Some best practices include:
- Compare prices across several suppliers while considering the reputation and quality of products.
- Look for warranties that guarantee the lifespan of the supplies.
- Read customer reviews to gather insights on product performance.
Understanding Warranty and Return Policies
When purchasing welding supplies, understanding the warranty and return policies can save time and money. Consider the following:
- Warranties: Assess how long the warranty lasts and what it covers (e.g., parts, repairs).
- Return Policies: Familiarize yourself with the return process in case the product does not meet your expectations.
Maintaining Your Welding Supplies
Tips for Proper Care of Equipment
Regular maintenance of welding supplies extends their lifespan and ensures optimal performance. Key maintenance tips include:
- Clean welding machines and tools after each use to prevent dust and debris buildup.
- Inspect cables and hoses for wear and tear regularly to avoid malfunctions.
- Store welding supplies in a dry environment to prevent rust and corrosion.
Signs Your Supplies Need Replacement
Recognizing when to replace your welding supplies is crucial. Common signs include:
- Frequent machine breakdowns, indicating wear and fatigue.
- Visible damage to protective gear, such as holes or fraying.
- Poor weld quality, suggesting that consumables are no longer effective.
Best Practices for Safety and Maintenance
In addition to maintenance, ensuring safety during welding operations is paramount. Consider incorporating these practices:
- Establish a regular training schedule to keep skills sharp and everyone updated on safety protocols.
- Ensure that all safety equipment is in good condition and readily available for all operators.
- Conduct periodic safety audits of the workspace to identify and rectify potential hazards.
Innovations in Welding Supplies
Emerging Trends in Welding Technology
As industries evolve, so do welding technologies. Notable trends include:
- Automation and Robotics: Introducing robotic welding systems to improve precision and efficiency in manufacturing lines.
- Advanced Welding Materials: Development of new alloys and filler materials that enhance weldability and properties.
- Smart Equipment: Integration of IoT technology in welding machines allows for better monitoring and data analytics.
Environmentally Friendly Supplies and Practices
The welding industry is moving towards more sustainable practices by considering:
- Using eco-friendly welding consumables that reduce fumes and emissions.
- Implementing recycling programs for spent materials and obsolete equipment.
- Adopting water-cooling technology that minimizes energy consumption.
Future-Proofing Your Welding Equipment
To stay competitive, it’s essential to future-proof your welding operations by considering:
- Investing in machinery that supports multiple welding processes to adapt to project demands.
- Keeping abreast of technological advancements in welding techniques and materials.
- Continuously upskilling the workforce through training and development opportunities.